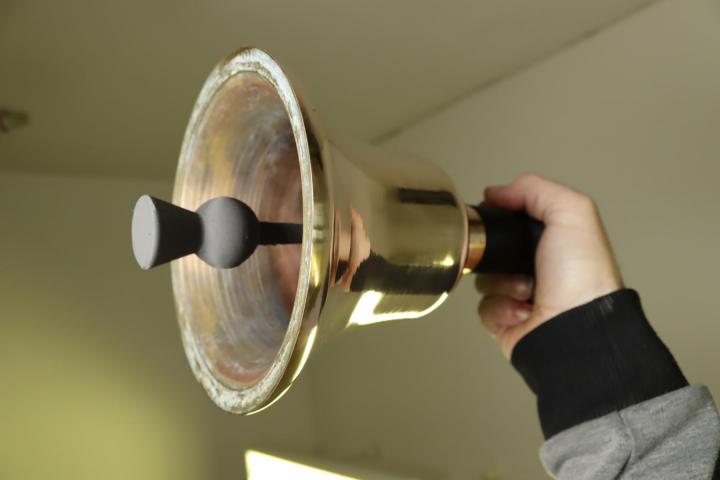
In this method, fine particles of metal or other materials are accelerated by gas to speeds of up to Mach 3 (approx. 3,700 km/h). Due to the high velocity, the particles bond tightly to the surface on impact and form a compact layer.
"The potential of the method lies in its ability to repair historically valuable bells. At the sites of the heartbeats, the bells wear out, forming impact craters that first affect the sound of the bell, then later concentrate the stresses and can lead to cracks and subsequent damage to the bell. Supersonic kinetization can produce a material that, although it does not reach the parameters of cast brass, is very close to them, as shown by our research carried out in cooperation with the Institute of Materials of the CAS v.v.i. and Impact Innovations GmbH," explains researcher Ondřej Kovářík from the Department of Materials of FNSPE.
FNSPE has been dealing with this issue for a long time and has already used its knowledge, for example, in the modification of the heart of Zikmund, the largest Czech bell.
Partners from the Czech Republic and abroad collaborated on the design and production of the bell model. The shape of the bell's rib was designed by Silesian University of Technology, which has experience, for example, in casting the world's largest bell, Vox Patris. The actual application of the material was carried out by the German company Impact Innovations GmbH, which is a leader in the field of supersonic coating. Its technologies are also being tested in the production of parts for Ariane rocket engines.
The final shape of the bell was created at the Institute of Plasma Physics of the CAS, which has the necessary technology and experience for the final modifications.
The finished bell received a composite steel-plastic heart, which was produced on a 3D printer at UJP PRAHA a.s. The whole bell is therefore made by additive methods.
A larger gallery of photos and a video of the bell's production process can be found here: Files - ownCloud@CESNET
FORMNEXT is the world's leading trade fair for additive manufacturing and next-generation industrial production. It will be held at the Frankfurt Exhibition Centre from 19 November 2024 - 22 November 2024.
The Department of Materials of CTU FNSPE is a scientific and pedagogical workplace that focuses on the study of failure of bodies and structures in basic and applied research. A wide range of scientific disciplines allows a comprehensive approach including fractographic, physical-metallurgical, fracture-mechanical, computational and statistical methods. The department includes a fractographic workplace, which addresses current problems, particularly in the energy and aerospace industries.