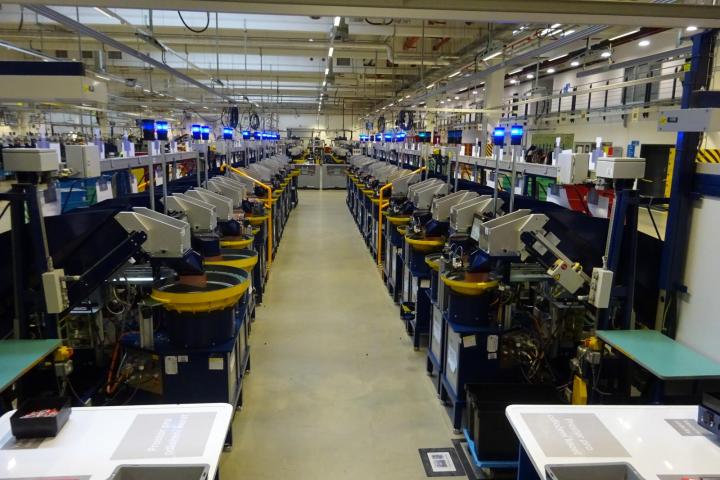
An example of cooperation is the current project concerning packaging lines, which have so far relied mainly on the experience and knowledge of operators. With the help of artificial intelligence, the concept of flexible and reconfigurable production lines is being developed, which help to respond quickly to changing market needs and seasonality of production. The specific output of the cooperation is a system based on data collection and analysis using machine learning methods to replace the routine work of operators in adjusting the vibrating drums. Based on the experience gained during the three-month test period, we can say that this solution will save 30% of operator time. As part of this pilot project, operators now have a more supervisory function and are alerted to emergencies using a newly developed mobile application.
"Modern factories built according to the principles of Industry 4.0 with the use of artificial intelligence make it possible to comprehensively solve tasks that line operators deal with on the basis of long-term experience, so-called emotion. Machine learning analyzes data flowing from production machines and looks for optimal settings for each of the huge number of possible combinations - according to the specific machine and its state of wear and the specific element dosed by the machine, "explains Professor Vladimír Mařík, scientific director of CIIRC CTU.
"Thanks to the close connection with production, we can test ideas and innovations directly in operation. This will give us not only real experience, but also feedback directly from fellow operators. Their knowledge thus brings a very practical view and expertise to the whole project, which cannot otherwise be simulated. Thanks to this cooperation between the academic world and real users, we are able to give ideas to life and at the same time naturally acquaint operators with the innovations we are working on. The Kladno factory is an innovation center for the entire LEGO group, so the functional solutions we develop in the Czech Republic will gradually expand to other LEGO® factories around the world, ”describes Josef Novák, director of the LEGO innovation team.
The proposed mobile application notifies the operator of a specific problem and at the same time reports data in summary. There is no need for the operator to be physically present on the line, he solves specific tasks where he is currently needed. This greatly simplifies his work. The functionality and use of the application will be further expanded.
"This research and development cooperation is also important from the point of view that the solutions designed by our team and tested at the Kladno production plant also help to advance the development of new technologies at the global level of LEGO. The Czech production plant and its innovation center is an example of the called out added value of Czech industry, "explains Petr Kadera, head of the intelligent systems for industry group at CIIRC CTU.
Being already in its demonstration phase, the project has shown great potential in reducing the workload for operators and increasing possible production capacity. The project was successfully approved by the top management at the end of March and will be put into pilot operation this year at the LEGO production plants in Kladno and China, and next year in Mexico and Hungary.